Speed vs Torque
The purpose of a rotary motor is to provide a desired rotational output speed while overcoming the various rotational loads resisting that rotational output (Torque). Speed and Torque are directly related, and are the two primary performance factors in properly selecting a motor for a specific application or use. To learn how to select the right motor to fit your application, the first step is to understand the relationship between speed, torque and output power of a motor.
Speed versus Torque
The output power of a motor sets the speed and torque performance boundaries of a motor, based on the equation:
Power (P) = Speed (n) x Torque (M)
-
- Power: The mechanical output power of a motor is defined as the output speed times the output torque and is typically measured in Watts (W) or horsepower (hp).
- Speed: The speed of a motor is defined as the rate at which the motor rotates. The speed of an electric motor is measured in revolutions per minute, or RPM.
- Torque: The torque output of a motor is the amount of rotational force that the motor develops. The torque of a small electric motor is commonly measured in either inch pounds (in-lbs), Newton meters (N-m) or other directly converted units of measure.
Since the rated output power of a motor is a fixed value, speed and torque are inversely related. As output speed increases, the available output torque decreases proportionately. As the output torque increases, the output speed decreases proportionately. This power, speed and torque relationship is commonly illustrated with a motor performance curve which often includes motor current draw (in Amps) and motor efficiency (in %).
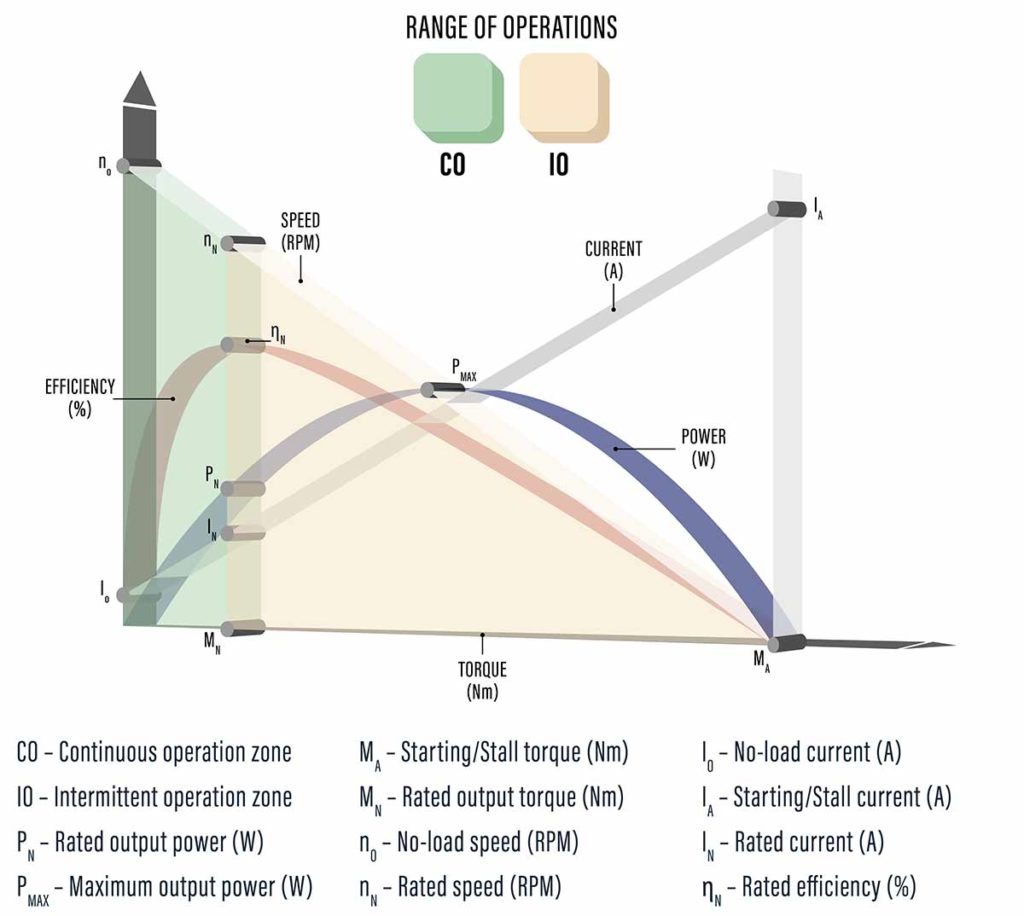
Speed and Torque Considerations for Electric Motor Selection
The key to selecting the right motor for a specific function is to first understand the requirements of the application. Since most motor applications are dynamic, meaning that torque and speed requirements change within the application, it is critical to define the various operating points within the application. Knowing or calculating the speed and torque requirements at each operational point in the application will determine the overall speed and torque requirements for the appropriate motor. Motor selection can be verified by plotting the various application operational points on the selected motor's performance curve to make sure that every speed vs. torque point falls within the appropriate zone of the curve (continuous or intermittent zones).
In many cases, application requirements will force the selection of a standard motor that is significantly oversized to ensure that all operational points are covered. Applying motors that are oversized for an application results in unnecessary cost, as well as larger and heavier designs of the overall product. Fortunately, custom motor suppliers can develop motors with optimized performance curves to precisely meet application requirements. This is done by changing the electromagnetic characteristics of the motor by altering either the wire size or the number of wire turns in the winding, or both. More turns of smaller wire provides more torque and less speed where fewer turns of larger wire provides higher speed but less torque. In some applications adding gearing to the motor output provides the ideal speed versus torque relationship while keeping the cost and size of the overall solution to a minimum.